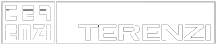

Nel 2007 Terenzi Srl rende possibile la realizzazione della lampada a sospensione Aeros, paradigma di ricercatezza estetica e virtuosismo tecnico. L'innovativo e raffinato design di Aeros, rappresentava una notevole sfida in termini produttivi. La prototipazione e l'industrializzazione della sua complessa struttura era stata proposta a diverse realtà produttive che però, per le esplicite difficoltà progettuali e tecniche riscontrate, avevano rinunciato alla commessa. Ross Lovegrove intendeva creare un oggetto etereo e fluttuante, percepito lieve nonostante le sue dimensioni. Aeros venne quindi ideata con un design curvilineo dato da due parti giustapposte, unite, realizzate in alluminio anodizzato e perforate come fossero ininterrotti delicati ricami circolari, tenuamente dorati. Questa elaborata trama superficiale si ispira alle forme della natura, ma la sorprendente texture, che origina un'elegante alternanza di luminosità e schermature, evoca anche reminescenze di antiche decorazioni Bizantine. La particolare diffusione della luce accentua con il suo effetto mistico, la sensazione dell'osservatore di trovarsi di fronte ad un oggetto oscillante e leggero, che affascina lo sguardo mediante riverberi molteplici: remissione orizzontale, attraverso il "trine" di alluminio che proietta le sue forme nell'ambiente, la diffusione diretta verso il basso e l'emanazione soffusa verso l'alto. Il riflettore infatti offre una distribuzione della luce morbida e rarefatta, in quanto il suo design è ispirato alla sequenza numerica di Fibonacci, teorizzata nel 1202 e intimamente Legata alla spirale logaritmica, rappresentazione della legge universale dell'armonia.
Tra il 2007 e il 2009, viene richiesto alla nostra azienda di ingegnerizzare, prototipare e produrre Aeros, Lampada a sospensione in alluminio anodizzato con fonte luminosa fluorescente compatta. L'alluminio, materiale indicato e prescelto da Lovegrove per la sua leggerezza intrinseca, una volta lavorato (imbutito, tranciato/tagliato, piegato), dovrà essere anodizzato con tonalità lievemente dorata "Golden Sand". La complessa struttura della lampada richiede in ogni fase operativa il superamento di particolari criticità, che sommate acuiscono esponenzialmente la difficoltà realizzativi dell'oggetto nonchè la logistica e lo stoccaggio. L'ingegnerizzazione diviene quindi estremamente importante e decisiva per la successiva messa a punto dell'industrializzazione del prodotto; prodotto che richiede anche standard qualitativi, e di conseguenza tecnici, assai elevati.
La struttura circolare di Aeros viene realizzata in due parti congiunte (superiore ed inferiore), con diversi processi e problematiche da superare. Lo schermo circolare inferiore ha come nota caratterizzante una doppia imbutitura molto profonda e di complicata realizzazione. Da qui ne consegue la scelta di un alluminio particolarmente duttile, che consenta lo stiramento estremo voluto dal design, senza cedere alla rottura. L'antitesi delle caratteristiche richieste, crea immancabilmente criticità, in quanto la plasmabilità del materiale lo rende particolarmente delicato e sensibile a graffi superficiali, intollerabili per lo standard qualitativo estetico del prodotto. Ne derivano quindi inevitabilmente altrettante specifiche attenzioni rivolte all'ottimizzazione e al monitoraggio dei passaggi finali di: imballaggio, stoccaggio e trasporto. I processi di lavorazione applicati allo schermo sono stati molteplici: dalla prima fase di taglio laser, alle imbutiture, ai diversi step di tranciatura, sino alla rifilatura e piegatura dei bordi. La produzione dello schermo circolare superiore ha previsto i medesimi passaggi sopra descritti, ad eccezione della seconda imbutitura, qui assente. Accomuna i due schermi l'ideazione di un'ingegnerizzazione sofisticata, utile alla messa a punto della rifinitura circolare dei bordi e soprattutto efficace al fine di realizzare il giro di perforatura a motivi decorativi, estremamente complessa in quanto compiuta sulla superficie convessa dei due schermi. La soluzione adottata per raggiungere il target di costo stabilito è stata un'elaborata tranciatura a stampo tridimensionale rotante, utilizzata sapientemente al posto della tecnologia alternativa offerta da laser 3D che, seppur all'avanguardia, necessita indispensabilmente di investimenti molto più cospicui e tempistiche meno rapide. L'ingegnerizzazione ha previsto anche l'ideazione e la fabbricazione di attrezzature speciali e stampi ad hoc per l'industrializzazione del prodotto. Ultimo processo altrettanto complicato è stato quello dell'anodizzazione, con la quale si sono vagliate e testate con svariate prove di metodo e tonalità, differenti cromie, sino al raggiungimento della gradazione ottimale desiderata e richiesta.