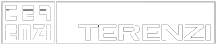

In 2014 the collaboration between TERENZI and DIMAC RED S.P.A. begins, a company that serves the European market with highly reliable electronic products, solutions, design and consultancy for various sectors (aerospace, automotive, railway, military, medical). Since August 2017 DLC BOX is being made.
DIMAC RED turns to TERENZI for the creation of a very complex "case", DLC BOX, useful for containing a battery for hybrid cars. The end customer is a leading company in the development, production, sale and assistance of a vast range of heavy, medium and light industrial vehicles. The innovative "Start&Stop" system, developed by DIMAC RED is functional to a significant reduction in consumption and emissions, in favor of energy saving and sustainability.
The product is divided into several parts, made of coupled plastic and metal. Alongside the advanced experience in metalworking TERENZI adds the know-how about plastic materials.
The materials used are talc-filled polypropylene, 5754 sheet aluminum and Bollhop inserts. TERENZI contributed to the design of the product, having regard to the construction constraints of the injection mold suitable for the production of the codes that make up the box and the two covers. There are two production moulds.
Great effort has been devoted to the correct drafting of the 3D mathematics to eliminate problems during the extraction phase. The mold includes some brass inserts which are mounted using pneumatic screwdrivers. The cover molds are among the most articulated, because there is also a part relating to the busbars.
The engineering carried out a fundamental step, performed with skill: the overmoulding of the busbars inside the "covers".
The busbars have been obtained by simplifying the aluminum electrical connection bars, where small parts on the market and other turned parts are specially mounted. The busbars are then cut with laser technology, some bent, and finally the small parts are assembled.
To complete the delicate passage of industrialization, we have foreseen the setting up of a dedicated space with all the equipment necessary for the assembly and testing of the products and molded parts. The assemblies of the first series were completed in the tooling department.