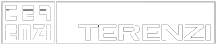

The start of the collaboration between our company, TERENZI SRL, and EMERSON AUTOMATION FLUID CONTROL & PNEUMATICS ITALY S.R.L EMERSON ELETRIC CO. (EMERSON Group) dates back to 1990. In all these years we have designed and manufactured molds, with which we have created hundreds of thousands of components then assembled by the client into its products, such as pressure switches and tanks for compressors.
Founded in 1890 with headquarters in St. Louis, USA, with more than 170 manufacturing locations worldwide, EMERSON is a global leader in the integration of technology, software, engineering and manufacturing. The integration is aimed at creating innovative solutions for customers operating in the industrial, commercial and consumer goods sectors.
Over the course of thirty years, with a circulation of approximately 10 million pieces, we have manifactured three components, an upper bridge and two stirrups, the Z1 and the Z5 respectively. These are technical components in galvanized iron (DC04 + white zinc plating), which have the function of facilitating the electromechanics of pressure switches and compressor tanks. These parts are then assembled by EMERSON into the following products:
- ASCO™ SOLENOID VALVE, DRY SERIES D144. Direct acting solenoid valve with total separation i.e. the fluid comes into contact only with the valve body and the "shutter" lever; it is suitable for the interception of liquid and gaseous fluids;
- ASCO™ QUICK COUPLING SOLENOID (DIN 46340) Z1 SERIES;
- ASCO™ QUICK COUPLING SOLENOID (DIN 46340) Z5 SERIES.
At the end of 2022, a detail was added to the two brackets and the upper deck, a bushing.
During the assembly phase, the two types of bracket are incorporated into the relative different coils; the small bushings are instead inserted into the holes on their surface. The function of these is mechanical, i.e. they keep the coil - a winding spool for the copper wire - centered and protected on the valve stem. Finally, the upper bridge is the indispensable component of the pressure switch; this measures the pressure in the compressor tanks. All the molds are designed and manufactured internally by our Tooling area: the elaborate 3-cavity mold that serves to shape the bush through the subsequent shearing process and the three progressive one-cavity molds required for the construction of the two brackets Z1 and Z5 and the upper bridge.
Maintenance and any changes to update the molds are always performed by the same division.
For the uprights of all the molds, the material used is 1730 steel, 2379, treated by secondary vacuum hardening and brought to a hardness of 60/62 HRC, for the dies, punches and blank holders.
The threading of some details such as, for example, the hole in the upper bridge, is performed at the same time as the shearing with a gear system. These rotate as the die descends (progressive with a single impression) directly into the 160ton double column press with lever drive.